Maintenance Tips for Spring Production Line Machinery: Prolonging Equipment Life and Efficiency
- mfmacauspring
- Nov 13, 2024
- 3 min read
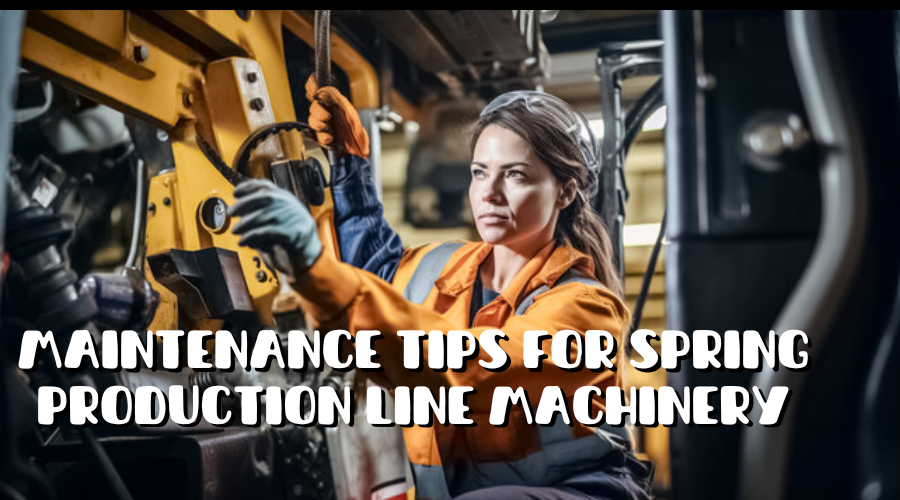
Behind every perfectly formed spring lies a complex symphony of machinery working in precise harmony. Like a well-oiled orchestra, each piece of equipment in a spring production line requires regular tuning and maintenance to perform at its peak. From the rhythmic motion of coiling machines to the controlled environment of tempering ovens, proper maintenance isn't just about preventing breakdowns – it's about ensuring the continuous production of high-quality springs that meet exacting specifications.
Critical Components of a Spring Production Line That Require Regular Maintenance
Spring production lines represent a significant investment, with each machine playing a vital role in manufacturing. The core equipment requiring consistent attention includes:
Coiling machines, with their intricate feed mechanisms and tooling
Tempering ovens with critical temperature control systems
Precision grinding equipment for achieving exact spring dimensions
Sophisticated inspection and testing equipment
Although each component's maintenance needs are unique, they form an interconnected system in which one machine's performance directly impacts the others.
Creating a Preventive Maintenance Schedule
A well-structured maintenance schedule serves as the backbone of equipment reliability. Consider implementing a three-tier approach:
Daily checks and basic maintenance
Weekly comprehensive inspections
Monthly deep-dive maintenance sessions
Document all maintenance activities in digital logs. This will make it easier to track patterns and analyze potential issues before they turn into costly repairs.
Daily Maintenance Checklist
Start each production day with these essential checks:
Visual Inspections:
Check for unusual wear patterns on tooling
Listen for abnormal sounds during the operation
Inspect wire guides and feeding mechanisms
Look for oil leaks or loose connections
Lubrication and Cleaning:
Apply lubricant to all specified points
Clean wire debris from feeding mechanisms
Remove any accumulated dust or metal particles
Check coolant levels and quality
Weekly and Monthly Maintenance Tasks
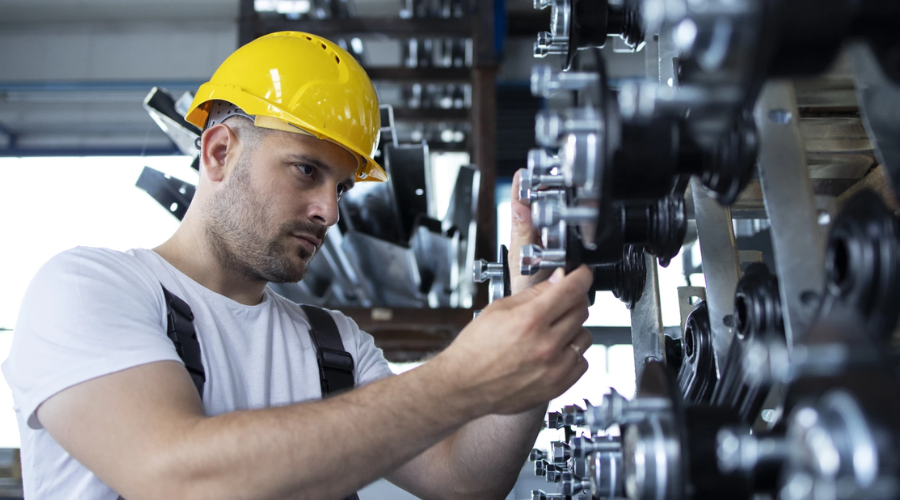
Weekly Tasks:
Verify alignment of all moving parts
Check and adjust belt tensions
Test emergency stop systems
Clean and inspect electrical cabinets
Monthly Tasks:
Perform comprehensive calibration checks
Update control system software
Replace worn tooling components
Conduct thorough safety audits
Long-Term Maintenance Considerations
Annual maintenance should include:
Complete disassembly and inspection of critical components
Replacement of all worn bearings and bushings
Verification of geometric accuracy
Update of safety systems to current standards
Training and Documentation
Effective maintenance relies heavily on well-trained staff. Implement:
Regular training sessions for operators
Detailed maintenance procedure documentation
Clear communication channels for reporting issues
Recognition programs for proactive maintenance practices
Embracing Predictive Maintenance Technologies
Modern maintenance approaches leverage technology through:
Vibration analysis sensors
Temperature monitoring systems
Power consumption tracking
Real-time performance monitoring
Frequently Asked Questions
Q: How often should coiling tools be replaced?
A: Depending on wire material and production volume, coiling tools typically require replacement every 3-6 months but should be inspected weekly for wear.
Q: What's the most common cause of unexpected downtime?
A: Poor lubrication and improper wire feeding alignment account for approximately 60% of unexpected stops in spring production.
Q: How can I determine the optimal maintenance schedule for my equipment?
A: Start with manufacturer recommendations, then adjust based on your production volume, operating conditions, and historical maintenance data.
Remember, consistent maintenance isn't just about preventing breakdowns – it's an investment in product quality, efficiency, and the longevity of your valuable equipment. By following these guidelines and adapting them to your specific needs, you can maintain peak performance in your spring production line while minimizing costly downtime and repairs. You can consult a trusted Spring Production Line supplier for any details or services.
Comments